The UK’s first fully autonomous dumpster truck (ADT) was put through its paces at a Devon quarry last week with designers hoping the technology will become a game-changer in the mining industry.
The massive, 40-tonne ADT (a converted Bell B40E) was showcased at the Cornwood quarry, one of Europe’s biggest opencast mines, where it was put to the test in dense fog and heavy rain driving at about 14 miles per hour - conditions that would normally prove impossible for a human driver.
Ben Uphill, operating director for the mining firm Sibelco, which operates the quarry, said that deploying fully autonomous trucks will have a positive impact on business.
“It’ll make things safer and more reliable, and keep our fuel use down. Ultimately, when you’re a global company you want to be as effective as you can. There are autonomous trucks elsewhere in the world, but this is the first in the UK.”
He said the move to a fully self-driven ADT had been partly motivated by truck driver shortages in the sector.
“Not a lot of people are coming into the industry, and there’s also the safety element when you’ve got human interaction,” he said.
Silica sand, ball clay and kaolin is mined at the site, which is used to manufacture ceramics for the sanitary industry – a multi-million pound business with an extensive worldwide demand.
The company’s aim is to have a full team of four ADTs by next year. The human element will remain, but it will be limited to having just one individual supervising the operation and ensuring the trucks run smoothly.
Unlike the camera-based system used in Tesla vehicles, which has proved to be accident-prone on various occasions, the software installed in the truck relies on an all-weather radar, which can operate without problems even when visibility is poor.
Dr. Chris Riedel, CEO of Xtonomy, a German-based company which designed the software for the vehicle, said: “The problem with the camera is that you have to run it through a neuro-network that you have to train, but you can train it only to react to something that it already knows.
“(By contrast) we use a radar system that sends out a signal and we get a reflection. It means it can detect obstacles and drive around them. This vehicle is so smart that it makes its own decisions to go from A to B – from the excavator to the dumping point.”
Dr Riedel said his company’s aim is eventually to have a “no-entry mine” where no humans have to enter. He however dismissed fears that the technology would ultimately result in job losses.
“We have not heard of a single client that has approached us that wants to reduce the workforce. The problem is rather finding the people who are willing to do such tasks.”
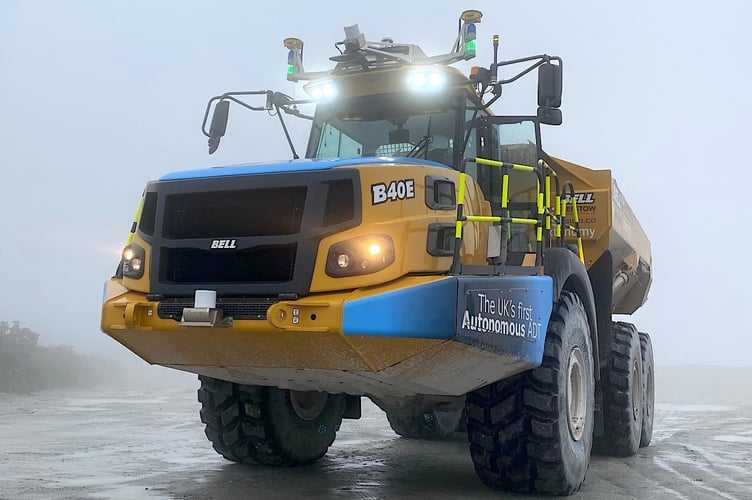